Dear Mr. Electrician: Is aluminum wiring safe to use? I am planning to have the electrical service to my house upgraded. The licensed electrical contractor that I am using will be installing aluminum wire for this installation.
Answer: It is safe to use aluminum wiring for new installations and upgrades.
Table of Contents:
NOTE: Some text links below go to applicable products on Amazon. As an Amazon Associate, I earn from qualifying purchases. Using my links helps to keep this website FREE.
Aluminum wire does have a questionable past, and problems still occasionally surface to this day from improper installations that date back to the 1960s and 1970s.
New types of wires, aluminum-rated devices, and equipment with aluminum wire approval have all been tested to be safe.
Click here to read a short history of “Aluminum Building Wire” published on Wikipedia.
ALUMINUM WIRING INSPECTION
There is no need to panic if you own a house built in the 1960s or 1970s and wired with aluminum throughout. However, you must take steps to ensure the wiring is properly installed and operating well.
The issues with the wiring at that time became apparent over time. It turns out that the alloys used to make that wire back then were subject to oxidation. As the oxidation at the connection points got worse, so did the resistance of the connection. This caused the connections to arc and burn, and the wired connection would melt with a low melting point.
When that became apparent, an anti-oxidant compound was then required on all aluminum wiring connections. However, the aluminum alloy has been changed. On new aluminum wiring installations, an anti-oxidant is not required unless specified by the manufacturer.
Another problem with aluminum was its greater expansion and contraction capacity than copper. So it would expand when the wire was under a large electrical LOAD, such as an electric heater. Then, when the LOAD was off, the wire would contract. Over time, this caused the connections under screw terminals to become loose, leading to arcing, burning, and melting.
When installing aluminum wire, it is very important that all connection and termination points are rated and approved for their use.
It is possible that a previous owner took the necessary precautionary measures to ensure that the existing aluminum wire was connected properly. However, you will have no idea if the repairs were done or done correctly unless you investigate or have an inspector or electrician take a look.
The simplest thing to do is look at your electrical switches and receptacles inside the electrical box. Turn off the power at the circuit breaker before doing this. If you remove the wall plate over a switch or electrical receptacle outlet, you may see the aluminum wires on the screw terminals. Shining a flashlight inside may help.
Try to see if an aluminum wire is connected directly to the screw terminal. Also, look inside the electrical box for purple-colored wire connectors commonly used for aluminum-to-copper wire connections.
Suppose you see copper wire on the screw terminals and purple connectors inside the electrical box. In that case, it is very likely that the particular outlet or switch was pigtailed correctly with copper wire and is safe from future aluminum issues.
The switch or outlet must be removed if you cannot see clearly inside the electrical box. This entails removing them from the wall with the power turned off at the circuit breaker box. This must be done very carefully where aluminum is installed.
Aluminum does not have the flexibility of copper. Consequently, it can break very easily upon removing a wiring device from the wall, making matters worse. If you are not comfortable with doing this, please call a licensed electrical contractor to have a look.
Aluminum conductors must be connected to a device approved for its use. It will have a Co/ALR designation on the switch or receptacle.
It is better to connect copper pigtails to the switch or outlet rather than directly connecting the aluminum to the devices. Copper wire is more flexible and can be bent many times before weakening and breaking. Aluminum will break after bending a couple of times. This is why it is more desirable to add copper pigtails.
I can speak from my own experience. After connecting an aluminum wire to an approved outlet, I pushed it back into the electrical box, and the wire broke. I now use stranded copper wire for pigtails for extra flexibility.
REPAIRING ALUMINUM WIRE CONNECTIONS
To make your existing wiring safe at every electrical receptacle and wall switch, the best procedure is to pigtail the aluminum conductors with copper wire. I usually use stranded copper wire for additional flexibility. Small aluminum conductors tend to break easily after only a couple of bends. Repairing bad wire connections can be accomplished using one or more methods.
The best and most recommended technique for aluminum wire repair is called the Copalum method. It is a specifically designed crimper for aluminum conductors. It uses a crimp sleeve designed and approved for this tool and the aluminum-to-copper connection.
The Copalum method is proprietary, and the user must be trained and licensed by the manufacturer to use the tool and purchase the necessary supplies. Consequently, you must call a licensed electrical contractor who has been factory-approved to make the necessary corrections to make your wiring safe using the Copalum method.
Not all electrical contractors have taken the time to get approved to use the Copalum method, so it may take several phone calls to find someone to do the work.
Another repair technique uses twist-on wire connectors specifically designed for aluminum and copper connections. Connecting stranded copper wire pigtails to solid aluminum wires is the best because it allows more flexibility for installing a wiring device and puts less strain on the aluminum conductors.
The aluminum connectors are more expensive than standard twist-on wire connectors but are tested and approved for aluminum and copper wire connections.
Another approved aluminum-to-copper connection choice is to use push-in wire connectors. These also cost more than regular push-in wire connectors.
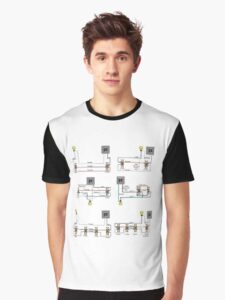
OXIDATION
Usually, when an electrician works with larger sizes of aluminum, he or she will coat the bare terminating wire end with a coating of anti-oxidant compound to stop one of the main problems with the old wire: oxidation.
Oxidation is no longer an issue with the newer aluminum alloys being sold, and an anti-oxidant is no longer required for new installations.
Some of my posts on old house wiring might be of interest.
To help keep this website FREE, please use this Amazon link for your purchases. As an Amazon Associate, I earn from qualifying purchases.
Click for a FREE copy of my book “Almost Everything You Need To Know To Repair a Bathroom Exhaust Fan In Your Home.”
Get your required “Emergency Disconnect, Service Disconnect” labels and stickers to satisfy the 2023 National Electrical Code requirements in article 230.85(E)(1) and (2) by going to my Redbubble Shop here.
Visit my Link Tree home page for my social media connections and other links.